Inconel 625
Inconel 625(UNS N06625) is a corrosion and oxidation resistant nickel alloy used for its high strength and excellent resistance to water corrosion. Its excellent strength and toughness is due to the addition of niobium, which along with molybdenum hardens the matrix of the alloy.
Alloy 625 has excellent fatigue strength and stress corrosion cracking resistance to chloride ions. This nickel alloy has excellent weldability and is often used to weld AL-6XN. This alloy is resistant to a variety of severely corrosive environments and is particularly resistant to pitting and crevice corrosion.
Content
Chemical composition of Inconel 625(%)
Element | Minimum(%) | Maximum(%) |
---|---|---|
Ni | remainder | remainder |
Cr | 20 | 23 |
Mo | 8 | 10 |
Nb | 3.15 | 4.15 |
Fe | - | 5 |
Al | - | 0.4 |
Ti | - | 0.4 |
C | - | 0.1 |
Mn | - | 0.5 |
Si | - | 0.5 |
Co | - | 1 |
P | - | 0.015 |
S | - | 0.015 |
Physical properties of Inconel 625
Property | Value |
---|---|
Density g/cm3 | 8.4 |
Melting range ℃ | 1290-1350 |
Mechanical properties of Inconel 625 alloy
Alloy Status | Tensile Strength Rm N/mm | Yield Strength RP0.2 N/mm | Elongation A5 % | Hardness HBW |
---|---|---|---|---|
Solid solution treatment | 760 | 345 | 30 | ≤220 |
Applications of Inconel 625
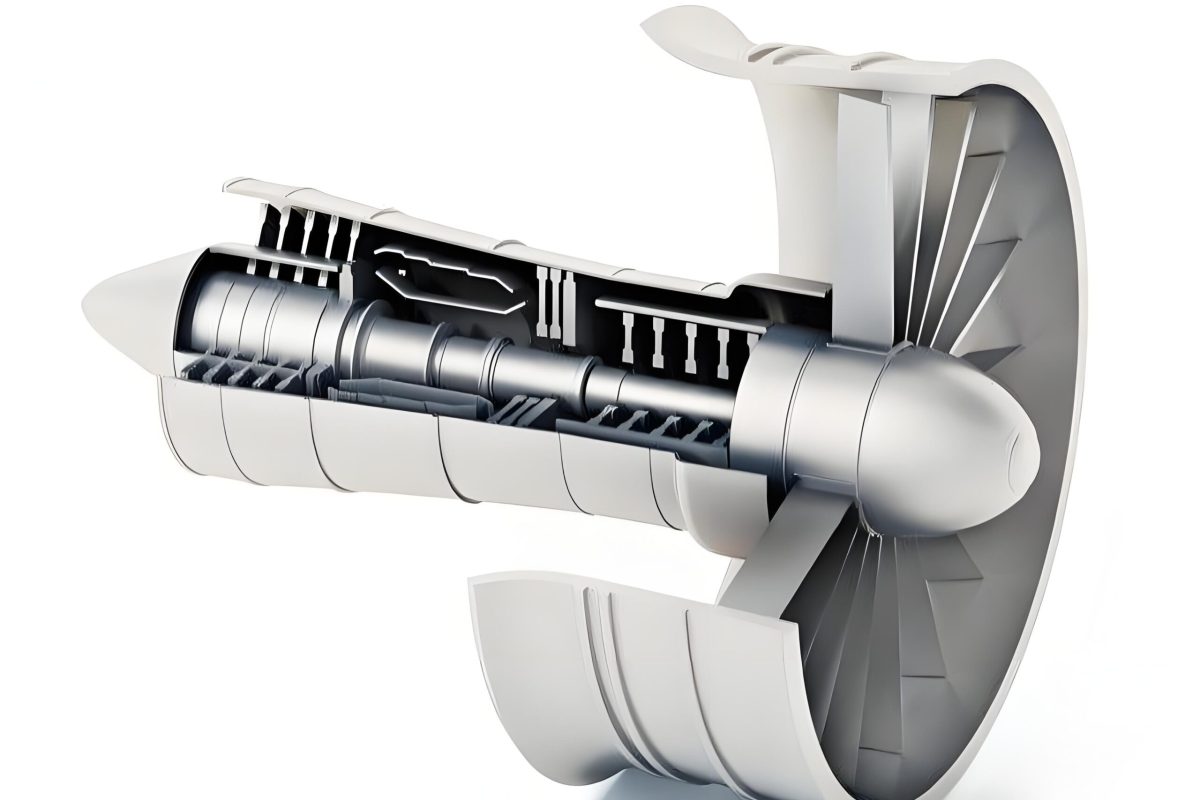
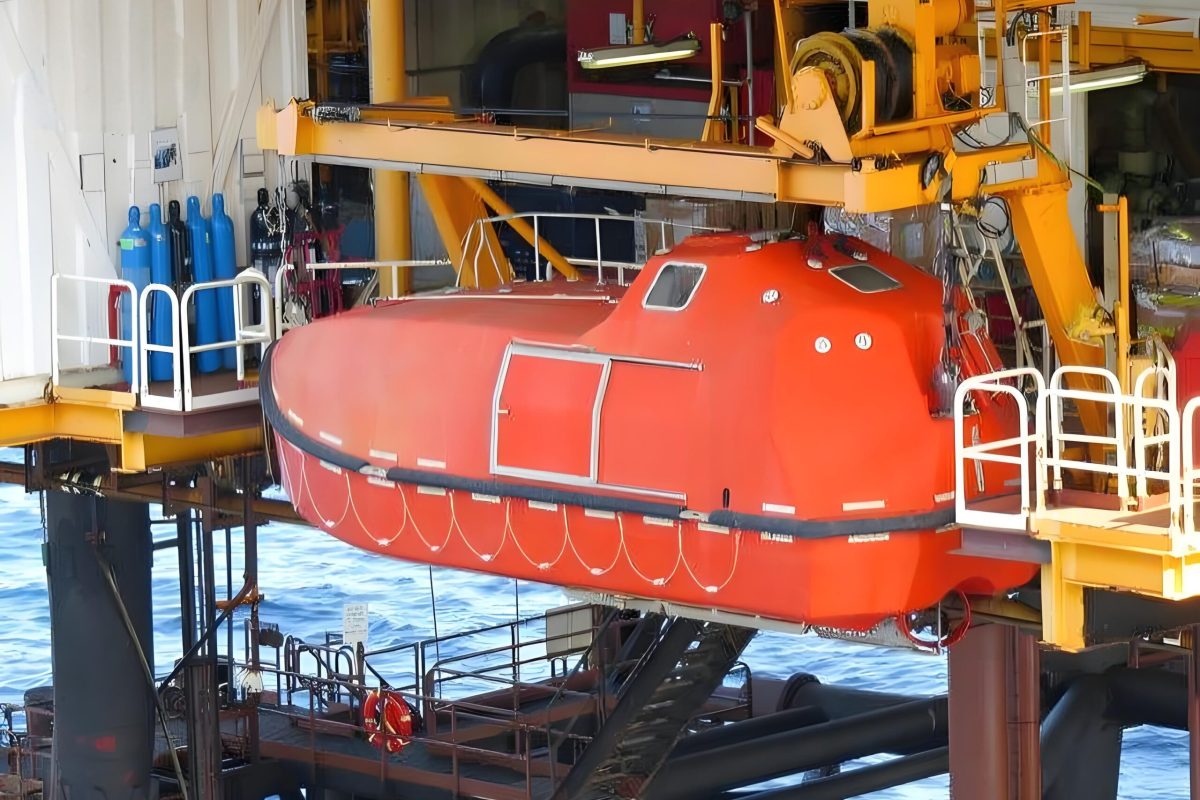
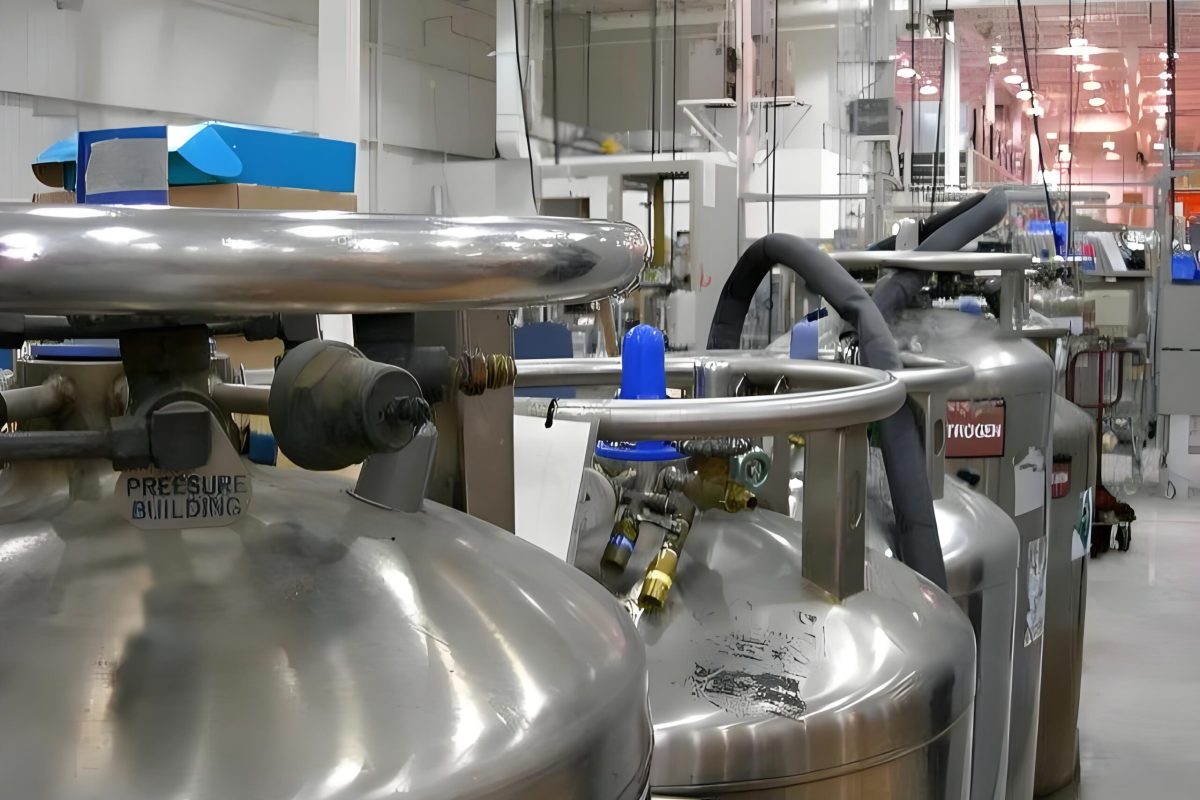
Inconel 625 (UNS N06625) is a highly versatile nickel-chromium-molybdenum alloy known for its exceptional resistance to corrosion and high temperatures, as well as its excellent mechanical strength and durability. Here are some key applications of Inconel 625, highlighting how its unique properties are utilized across various industries:
Aerospace Industry:
- Jet Engine Components: Utilized in exhaust systems and turbine blades due to its ability to withstand high temperatures and oxidation.
- Spacecraft Components: Used in rocket engine thrust chambers for its thermal stability and resistance to high-heat environments.
Marine Industry:
- Submarine Rescue Systems: Employed in submarine rescue devices and other deep-sea exploration equipment because of its excellent corrosion resistance in seawater.
- Propeller Blades and Underwater Equipment: Suitable for propellers and submersible vehicles due to its strength and resistance to chloride-induced stress corrosion cracking.
Oil and Gas Industry:
- Offshore Oil Rig Components: Used in risers, underwater piping systems, and other offshore platform applications where strength and corrosion resistance are essential.
- High-Pressure Environment Equipment: Ideal for components such as valves, pumps, and heat exchangers in sour gas environments due to its resistance to sulfide stress cracking.
Chemical Processing:
- Reactor Vessels and Piping: Utilized in chemical reactors and piping systems for handling mixed acids and other highly corrosive materials.
- Flue Gas Desulfurization Systems: Applied in systems for controlling emissions in power plants because of its resistance to a variety of acidic compounds.
Nuclear Field:
- Nuclear Reactor Cores and Control Rods: Chosen for nuclear reactors due to its excellent mechanical strength and resistance to radiation damage.
- Waste Re-processing Equipment: Utilized in handling radioactive materials, providing safety against corrosion by radioactive elements and high temperatures.
Automotive Industry:
- Exhaust Systems: Used in high-performance vehicle exhaust systems due to its high-temperature strength and oxidation resistance.
These applications are directly tied to the alloy’s key properties, such as high tensile and yield strength, excellent fatigue and creep resistance, and its unparalleled performance in extreme environments. This makes Inconel 625 an ideal choice for critical applications where failure is not an option.