Inconel 718
Inconel 718 alloy is a precipitation-hardening nickel-chromium-iron alloy containing niobium and molybdenum, with high strength, good toughness, and corrosion resistance at both high and low temperatures up to 650°C. Inconel 718 alloy is available in either a solid-solution or precipitation-hardened state.
Content
Chemical composition of Inconel 718(%)
Element | Minimum(%) | Maximum(%) |
---|---|---|
Ni | 50 | 55 |
Cr | 17 | 21 |
Fe | remainder | remainder |
C | - | 0.08 |
Mn | - | 0.35 |
Si | - | 0.35 |
Mo | 2.8 | 3.3 |
Cu | - | 0.3 |
Co | - | 1 |
Al | 0.2 | 0.8 |
Ti | 0.65 | 1.15 |
Nb | 4.75 | 5.5 |
B | - | 0.006 |
P | - | 0.01 |
S | - | 0.01 |
Physical properties of Inconel 718
Property | Value |
---|---|
Density g/cm3 | 8.24 |
Melting range ℃ | 1260-1320 |
Mechanical properties of Inconel 718 alloy
Alloy Status | Tensile Strength Rm N/mm | Yield Strength RP0.2 N/mm | Elongation A5 % | Hardness HBW |
---|---|---|---|---|
Solid solution treatment | 965 | 550 | 30 | ≤363 |
Applications of Inconel 718
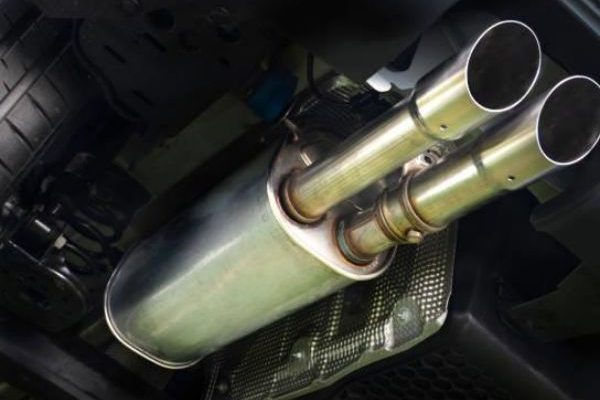
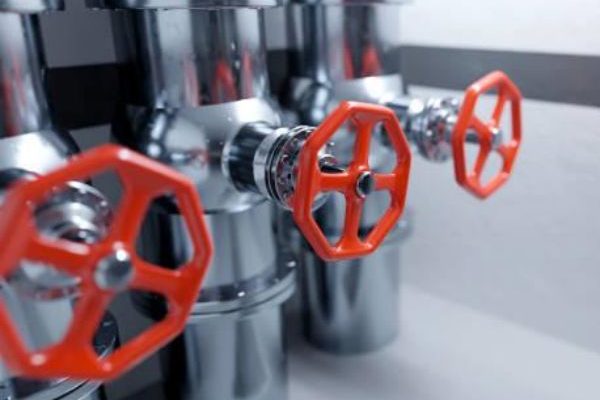
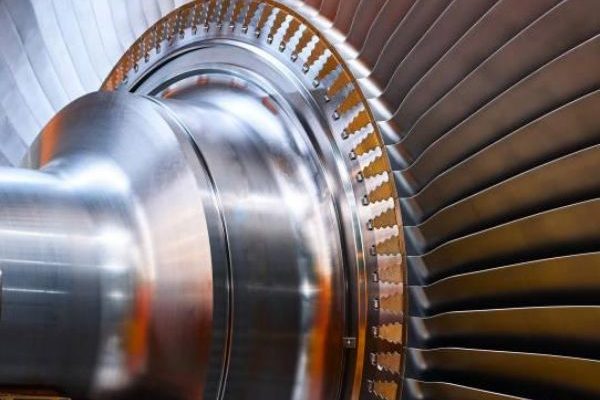
Inconel 718 is renowned for its exceptional strength, corrosion resistance, and ability to retain mechanical properties at high temperatures. These unique properties make it ideal for a range of specialized applications, particularly in extreme environments. Here are some key applications where Inconel 718’s unique properties are especially beneficial:
Aerospace Industry: Inconel 718 is extensively used in the aerospace sector for manufacturing turbine engines and rocket components. Its ability to withstand extreme heat and pressure makes it ideal for critical parts like turbine blades, discs, casings, and engine exhaust systems. The alloy’s resistance to thermal fatigue and oxidation at high temperatures ensures the reliability and longevity of aerospace components.
Gas Turbine Applications: Beyond aerospace, Inconel 718 is used in industrial gas turbines for power generation. Components such as turbine blades, seals, and combustion chambers benefit from the alloy’s high-temperature strength and corrosion resistance, which are crucial for efficient and reliable energy production.
Oil and Gas Industry: In the harsh environments of oil and gas extraction and processing, Inconel 718 is used for its resistance to sour gas, pitting, and crevice corrosion. Components like valves, fasteners, and various drilling and completion equipment can withstand the corrosive effects of hydrogen sulfide and other challenging conditions found in this industry.
Nuclear Reactors: The material’s resistance to post-irradiation ductility loss makes it suitable for components in nuclear reactors, where maintaining structural integrity is crucial for safety. Inconel 718 is used in reactor cores and control rods, offering durability and stability in a radioactive environment.
Cryogenic Applications: Due to its excellent mechanical properties at very low temperatures, Inconel 718 is a material of choice for cryogenic storage tanks, transportation of liquefied gases, and other applications where structural reliability is essential in extreme cold.
High-Performance Automotive: In the automotive industry, especially in the realm of high-performance and racing vehicles, Inconel 718 is used for exhaust systems and turbocharger components. Its ability to withstand high temperatures and corrosive environments helps improve engine efficiency and durability.
These applications highlight Inconel 718’s unique properties, making it an indispensable material in industries that demand exceptional performance under extreme conditions.